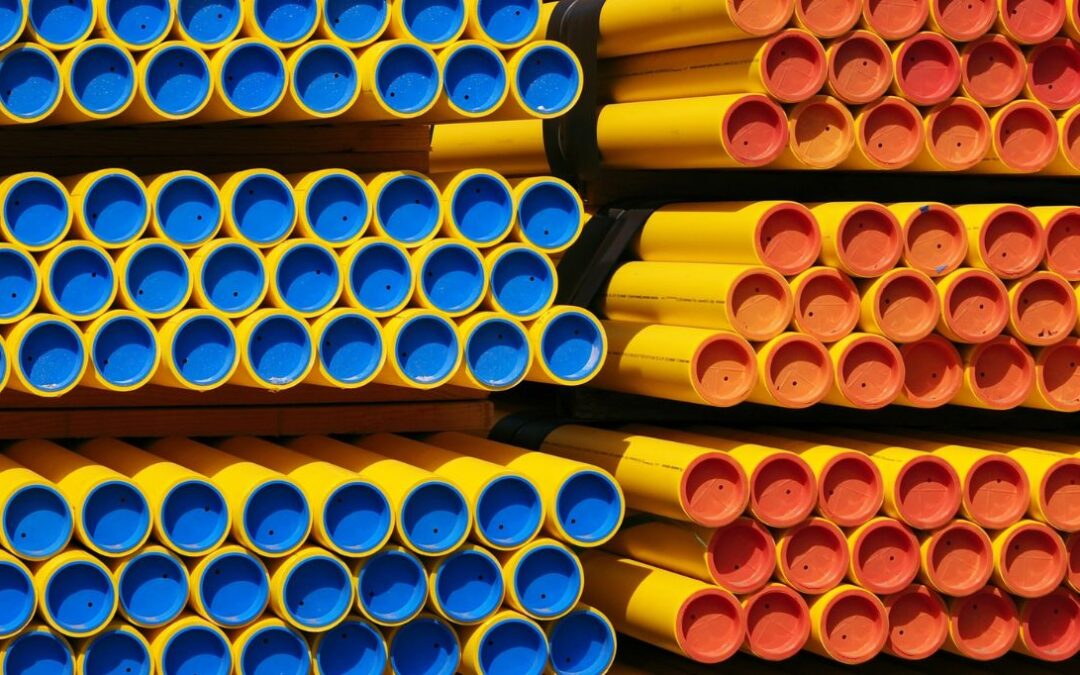
The ability to mold, customize, and adapt thermoplastics repeatedly makes them a frequently used material in industrial manufacturing. They are widely used for solar, automotive, and appliance manufacturing. With plastic extrusion, manufacturers can create parts for diverse applications. Here are four features of thermoplastics:
Reusability and Malleability
Manufacturers use plastic extrusion to melt, reshape, and solidify thermoplastics without changing their structural integrity. This reusability helps companies achieve sustainable manufacturing, especially in high-demand industries. Automotive manufacturers can easily create complex parts with intricate designs, such as instrument panels, buttons, and cup holders. These plastics can also be used to make building materials like fencing and decking.
The material’s flexibility offers consistent results when refining prototypes over multiple iterations. It lowers production costs and waste because companies do not have to produce new materials. Thermoplastics can also be poured into a shaped die to form customized parts like tubes, sheets, and profiles.
Chemical Resistance
Chemicals like acids, alkalis, and solvents may cause immense damage or corrosion to non-resistant materials. Thermoplastics can replace parts commonly damaged due to corrosion because they are resistant to chemicals and other substances. Medical equipment uses chemical-resistant plastic parts to maintain functionality when exposed to sterilizing chemicals and cleaning agents.
The automotive sector also needs chemical-resistant parts that can withstand exposure to oils, gasoline, and engine chemicals. Manufacturers in these industries use polypropylene and polyethylene to reduce chemical corrosion. Thermoplastics in fuel tanks and pipes stop contaminants from leaking into vehicle systems.
Impact Resistance and Durability
Thermoplastics withstand immense mechanical stress and pressure in industrial use. Their toughness allows them to absorb impact without fracturing or breaking. In industries where components are subjected to frequent or sudden forces, extruded parts offer structural integrity, long-lasting durability, and uniform density. Some components that meet these requirements include automotive bumpers, interior panels, dashboards, helmets, and other protective gear.
Many motorists prefer the protection of high-impact thermoplastics that absorb shocks during collisions. These components are also lightweight and resilient, maintaining their structure upon impact. Reducing the overall weight also improves fuel efficiency. In the solar industry, high-impact frames and mounting systems retain their strength and shape with high loads.
Thermal Stability
Thermoplastics excel in environments with frequent or extreme temperature variations. In applications like engine components, food processing, and aerospace industries, these plastics do not degrade or warp at high temperatures. The materials maintain structural integrity and boost the overall performance of components. In the automotive sector, thermoplastics make durable under-the-hood components that receive heat transfer from the engine or other moving parts. On solar panels, they provide thermal stability to resist heat-related degradation in regions with extreme climates.
Enjoy Better Plastic Extrusion Using Thermoplastics
Thermoplastics are reusable, malleable, chemical-resistant, impact-resistant, durable, and excel in thermal stability, making them key components in various industries. These features enable them to contribute to sustainability and environmentally conscious manufacturing. An experienced manufacturer can review your project requirements and industry standards to recommend the best designs and materials. Contact a plastic extrusion expert today to start using products made with thermoplastic components.